A wide range of technologies including augmented reality and virtual reality will be used to project the visitor forward into the future to create an immersive theatre experience. “This is not the museum where you will see objects in cases with labels next to them,” says Carlson. “In a lot of the main galleries, there will be no labels at all. It will be a completely immersive experience that engages the visitor as a really important contributor to the experience, rather than as a viewer of someone else’s work.”
He hopes to offer an optimistic view of the future as a counterpoint to what he considers as a generally bleak outlook presented by the entertainment industry. “We want to show how people might creatively respond to the challenges, while at the same time being realistic about the challenges that are coming,” he says.
One floor will showcase the expected near-future gadgets, but the focus will still be on technology that will bring a benefit to humanity, whether by helping to feed the world, meet our water needs or make transportation more sustainable.
The Museum of the Future is hoping to attract more than one million visitors a year, with half coming from outside the UAE.
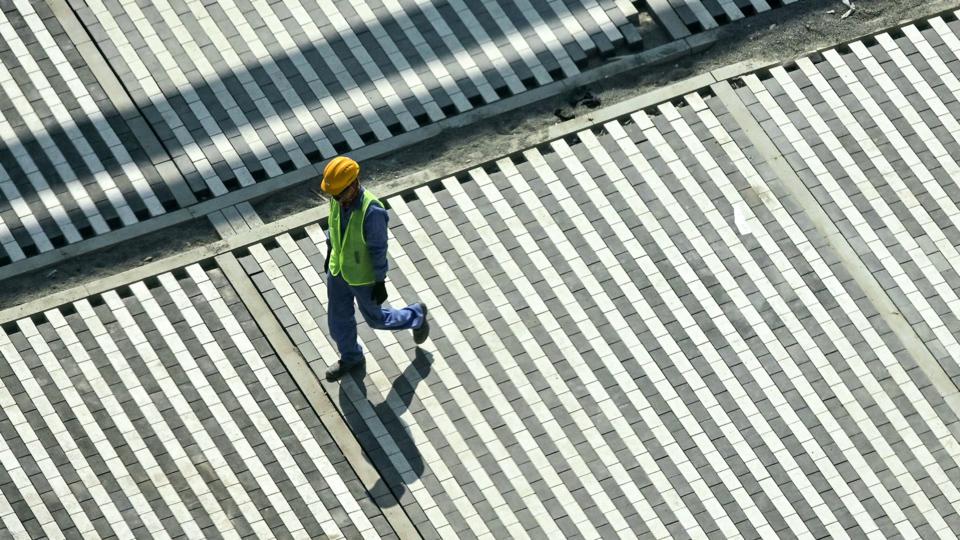
Construction still has a long way to go before the focus shifts inside at the end of the year. But the team recognises that the exhibitions need to be as impactful as the building that will house them, if not more so.
Still, Bauly hopes the museum will become an exemplar of how a modern building should perform. Its unconventional shape has meant absolutely everything has been modelled, analysed and optimised in advance, from fire evacuation and smoke extraction strategies to the cleaning of the exterior. Parametric modelling of people movement throughout the building was used to determine how to reduce queuing times and help flow with the width of corridors, number of lifts, design of the bathrooms and layout of the ticketing hall. And all the data from the design and construction phases will go on to inform the operation and maintenance of the museum.
Bauly says he has many lessons to take forward to his next project. “It is all the things we have spoken about for years, like good MEP, sustainability, the structure being clever and integrated, optimised solutions. These are not just about driving down the cost for the client, but how the building performs in terms of safety and people’s health and welfare.
“Everything we have ever known about doing buildings has changed within the space of this one project, because the project demanded it. Otherwise, we couldn’t have solved the challenges that came as a result of the shape. It has changed how we work and that is great for the industry moving forwards.”
Even before opening, it seems, Dubai’s Museum of the Future has become a showcase for future technology building design.
Credit : BBC.com